Application and design considerations for media packaging and lamella in water and wastewater treatment professional workshop by the Italian company Refill-Tech and in collaboration with the Spinas engineering group, with the presentation of Mr.Mark Izard and Mr.Gabriele Caccia was hold on Tuesday, February 3, at the site of the Society of Specialized Consulting Water and Wastewater Custodial Engineers and Consultants with an Introduction to packing media application, bioxidation and MBBR media, lamella applications in settling systems and conditions for packing and maintenance of lamella, and for second time it was hold on Wednesday, February 4, at the Research Center of Oil Industry with the concentration of packing media and lamella applications on cooling tower sections and related equipment in the Refining and petrochemical industries of Iran.
The 13th International Water and Wastewater Exhibition of Iran, 16-19 October 2017
The Spinas Engineering Group is expected to welcome visitors at the 13th International Water and Wastewater Exhibition of Saloon 1-44, with the presenting the new solutions in the field of wastewater and waste recycling technologies.
Partner companies :
- PROBIG: Non-metallic chains and oven systems (DAF, CPI, API) from Austria.
- IN-EKO: Producer of the Water and Wastewater Treatment Plant equipment. Specialization in Microfiltration (Drum filters, Disc filters – for TSS, parazites and P removal) and combined pre-treatment systems with Multifunctional pre-treatment (for screensnings, sand and FOG removal).
- AQUA ENGINEERING: technical and executive partner of RO projects and water and wastewater treatment plants from Austria.
Iranian Water and Wastewater Science and Engineering Congress
SPINAS will attend the Iran’s Water and Wastewater Science and Engineering Congress on February 14 and 15, 2017. Our booth at the Congress Fair welcomes experts and specialists to introduce the technologies of water treatment plants and wastewater such as MBR, SBR, DAF ….
https://nwwce.ut.ac.ir
12th International Water and Wastewater Exhibition, October 25-28, 2016
Spinas Company attended the twelfth Iranian International Water & Wastewater Exhibition of Tehran-Iran.
We are proud that more than 400 people visited the Spinas booth.
Visitors were informed about Spinase’s extensive activities and the latest technology in the water and wastewater industry.
www.watex.ir
Advanced Sequencing Batch Reactor ASBR
- The best choice for high-quality wastewater treatment and minimum investment and operation cost is the advanced SBR Advanced Technology (ASBR).
ASBR has a registered record in terms of performance on a global scale.
ASBR is an optimized biological process for most domestic, municipal and industrial refinement units. This system has been successfully implemented for small, medium and large urban areas. ASBR is used for modular development, replacement and upgrading of existing refinery capacity as well as a pre treatment for the strong industrial wastewater.
Urban and domestic waste water applications:
- Rural communities, towns and cities
- Airports and military centers
- Commercial and residential buildings
- Schools, hospitals and large stores
- Septic tanks waste water treatment
- Residential centers and hotels
- Restaurants and recreational centers
- Apartments and complexes
Industrial applications:
- Food and drink
- Paper and textile
- Petrochemicals, refineries and paints
- Wastewater from anaerobic treatment
- Pharmaceutical and sanitary
- Electronic
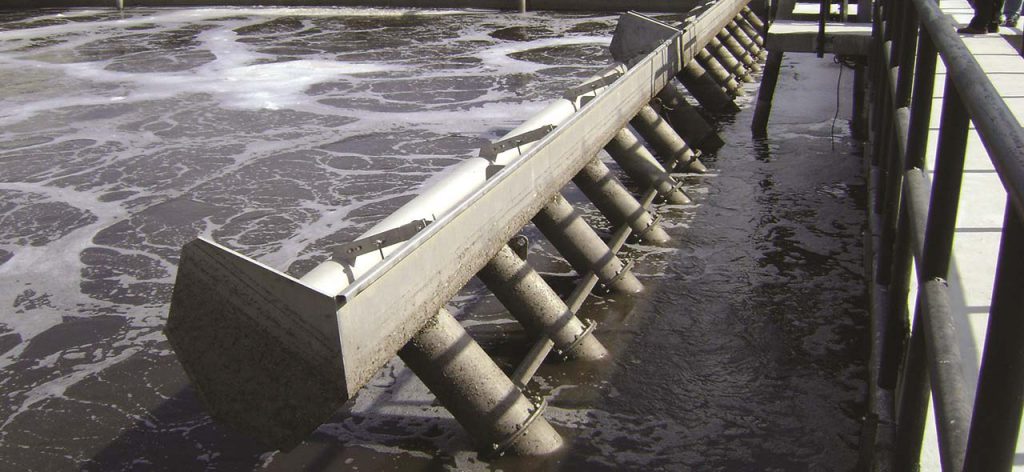
ASBR process and design capabilities:
- Increasing the proper formulation of solids and, at the same time, preventing the bulking process because of the ability to select biological regions that will lead to a high quality of treated wastewater.
- The removal of biological nutrients includes nitrification, denitrification and phosphorus removal
- Less tanks and less space occupancy compared with conventional sludge treatment by up to 30%
- High aeration efficiency and reduced energy consumption
- The minimum equipment will be easy to maintain and easy to operate.
- Strong stainless steel latches provide long and reliable durability.
- Freely selectable rectangular, square, circular, single or multiple tanks make this system flexible.
- Capacity from 20 to 190 thousand cubic meters per day.
- After the commissioning of the wastewater treatment plant, after-sales services will include an evaluation and analysis of the output data from the refinery to ensure optimal process performance. In addition, connecting to the Internet port and through SCADA on the control panel provides remote service capability.
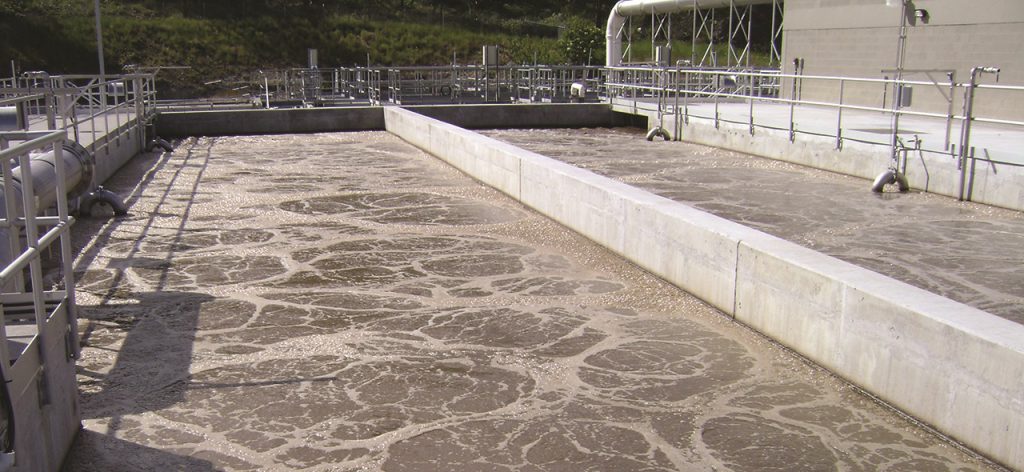
Consulting services for SBR processes and equipment:
- Conceptual, Primary and Detailed Process Design
- Manufacturing and supplying equipment
- Project management services during implementation
- Collaboration during launch
- Personnel training services
- After-sales service and customer support
Operation and maintenance services - Process optimization
- Remote control and data analysis
- Evaluation of system performance
Operation of the cassette filter type MBR modules
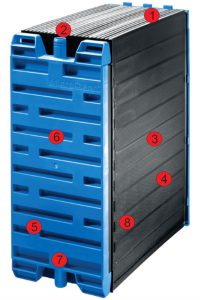
Principle of filtration
Water containing solid particles flows through the filter cloth/sieve of the given structure which has openings of a certain size. The filter cloth traps impurities which are bigger than openings in the filter cloth while smaller particles, including water, flow through the filter out. As the filter cloth slowly becomes clogged by the increasing amount of filtered impurities, the filter cloth must be backwashed so it can work again.
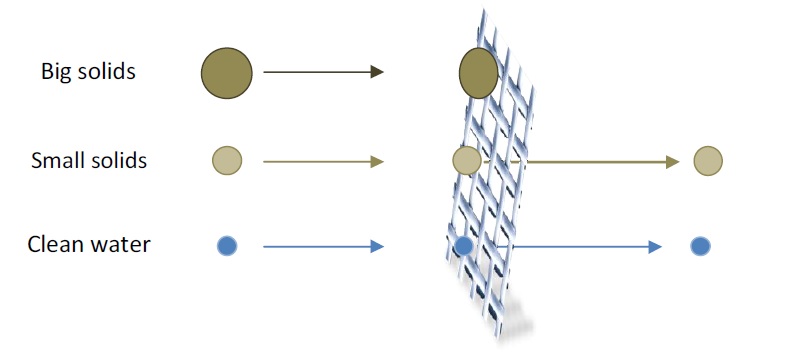
SS (mg/l), mesh (micrones)
Suspended solids (SS) are in mg/l and show how many SS (e.g. flocs and other debris) are in one liter of water. It is just a reference parameter. It is also important to know what solids look like and select the mesh accordingly.
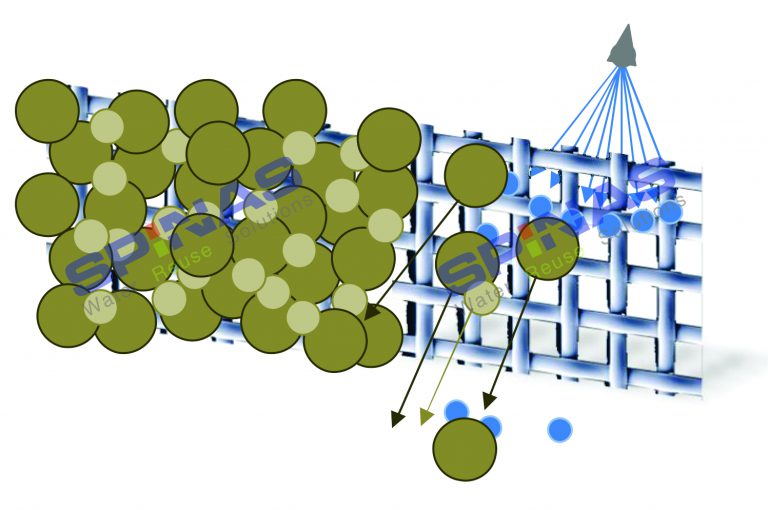
Secondary filter layer
Filter capacity is greatly influenced not only by the volume but also by the nature of filtered SS. What matters is their size (flat particles tend to clog openings more easily than round ones), mechanical strength (compact particle can be filtered better than non-compact slimy ones) and the proportion of small and big particles in the total volume of influent. If a certain number of compact solids, bigger than the mesh openings, occur, it can result in a thin layer of sludge – secondary filter layer, which is capable of catching solids which are considerably smaller than the size of mesh openings. It is therefore advisable to choose a filter with a greater filter area so the filter idle time is as long as possible and an efficient secondary filter layer can form on the inner side of the mesh. This layer is flushed down to the sludge channel during backwash.
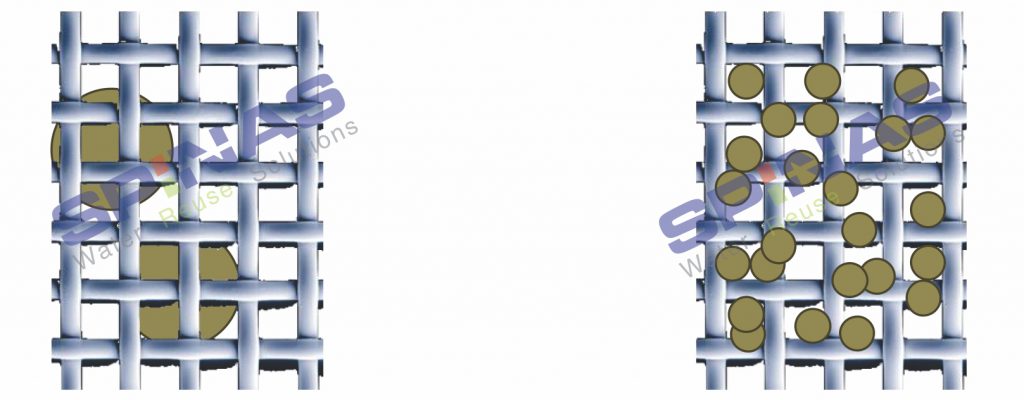
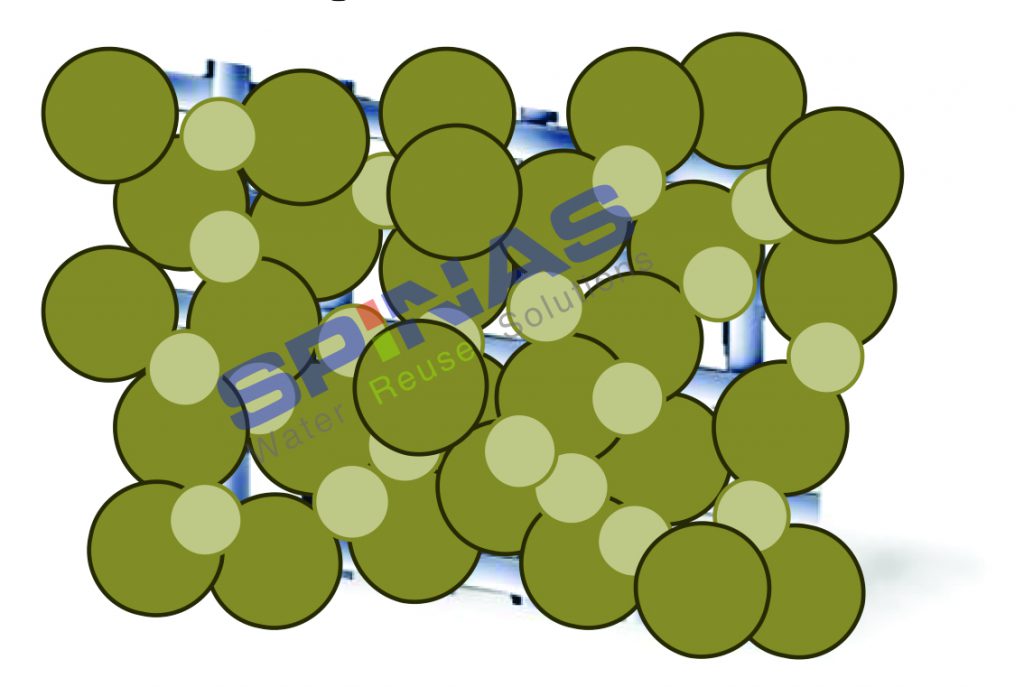